How important is it to have a Quality Management System in place?
23 Jun, 20235 minutesQuality Management Systems (QMS) are essential for maintaining consistency, regulatory compl...
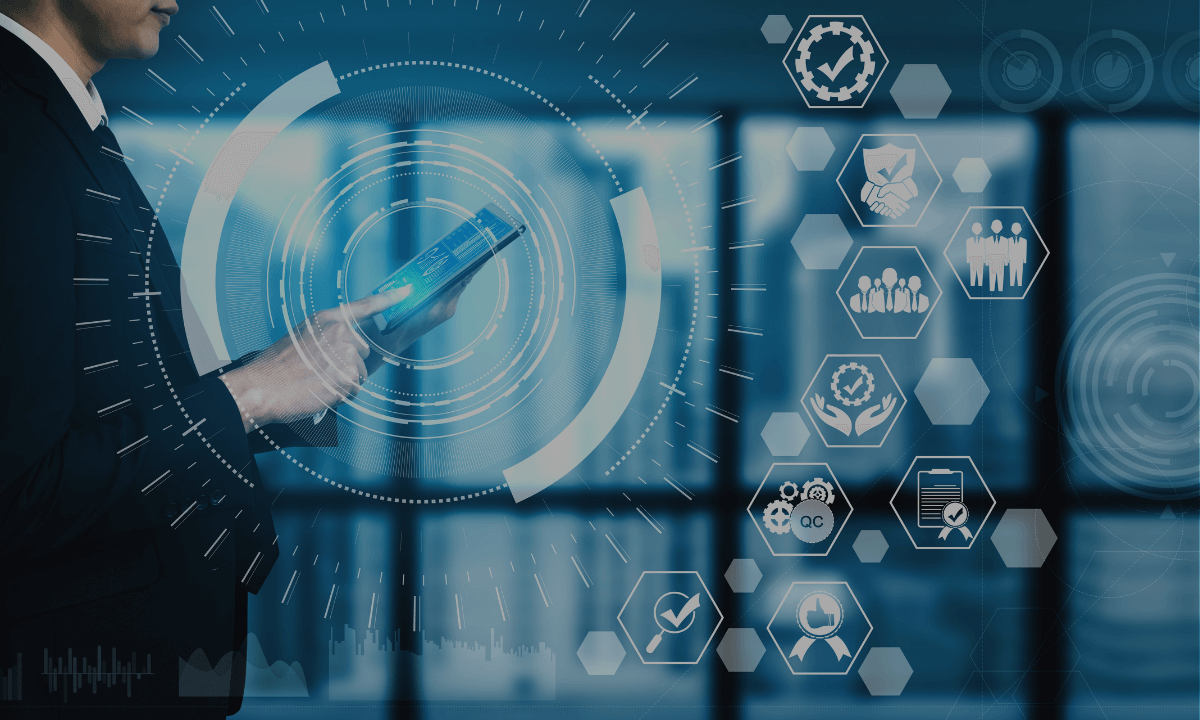
Quality Management Systems (QMS) are essential for maintaining consistency, regulatory compliance, and quality control in life sciences. Companies lacking a QMS often rely on ad-hoc practices, which can lead to increased risks and inefficiencies. Here are the benefits of implementing a robust QMS.
The Benefits of Implementing a Quality Management System
1. Standardised Processes
A QMS standardizes processes across the organization, ensuring consistency in operations. Standardization reduces errors, aids in training, and maintains high-quality standards.
2. Enhanced Product Quality and Safety
A dedicated QMS provides systematic quality control, risk management, and traceability, ensuring products meet quality standards and reducing the risk of defects. This focus on quality enhances company reputation and customer trust.
3. Regulatory Compliance
QMS frameworks ensure compliance with Good Manufacturing Practices (GMP), Good Clinical Practices (GCP), and other regulations, demonstrating a commitment to quality during audits and inspections.
4. Continuous Improvement
With a QMS, companies can continuously monitor performance metrics, identify areas for improvement, and optimize processes, leading to increased efficiency and product quality.
5. Risk Management
A QMS integrates risk management, helping companies proactively identify, assess, and mitigate operational and product risks to minimize incidents and losses.
6. Improved Efficiency and Productivity
Streamlined guidelines, roles, and responsibilities improve productivity, eliminate inefficiencies, and enhance resource utilization, enabling timely product delivery.
7. Customer Satisfaction and Trust
A commitment to quality through QMS fosters customer satisfaction, handling complaints efficiently and enhancing customer relationships.
8. Organizational Alignment and Communication
A QMS enhances communication across the organization, aligning employees with quality objectives and creating a shared commitment to quality.
Why Use a Consultant for QMS Implementation?
Hiring a consultant can provide expertise, save time and resources, and ensure a well-aligned QMS. Here are the benefits of working with a consultant.
1. Expertise and Industry Knowledge
QMS consultants bring specialized knowledge of life sciences, regulatory landscapes, and best practices, allowing them to design a tailored QMS for your business.
2. Time and Cost Efficiency
Consultants expedite the implementation process, avoiding pitfalls and guiding you through each step efficiently, saving both time and costs.
3. Objective Perspective
With an external, unbiased viewpoint, consultants can assess your current practices, pinpoint gaps, and recommend effective solutions.
4. Regulatory Compliance Assurance
Consultants stay updated on regulatory changes, ensuring your QMS aligns with the latest compliance standards and avoids costly delays.
5. Training and Change Management
Consultants provide essential training and change management support to ensure smooth adoption of the QMS by effectively communicating benefits and objectives.
Is it Time to Implement a QMS?
A Quality Management System brings essential benefits in maintaining product quality, achieving regulatory compliance, and building customer trust. Let’s discuss how a QMS can elevate your business and how we can support you in this process.